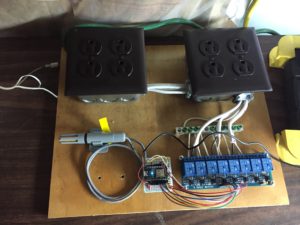
I’ve been so busy DOING this project that keeping updates here has eluded me. I had previously written about the Food Computer concept being deployed by the MIT Media Labs Open Agriculture Initiative. I was keeping an eye on the progress over there, intending to build one of their systems. I decided to temporarily “do my own thing” for a couple of reasons. For starters, their system is in development, and jumping in now requires a level of knowledge that escapes me. I’m just not up to speed on the level of software development required to use their approach right now. Second, I have decided that building my own setup based on a traditional hydroponic system has more value and efficiency for me at this juncture. I eventually hope to have a system that is 100% compliant with the MIT approach, so I can contribute to the data gathering, educational, and community based initiatives they are so gallantly spearheading.
So, why go your own route?
As I mentioned, my software development abilities drift far behind my hardware abilities. I am a bit lost looking upon the sea of code that MIT has out there. I have already put a number of the pieces together in preparation, but I knew my own approach would be a less frustrating way to actually get results. Reason number two is cost. By some estimates, the food computers can quickly run between $2,000 and $3,000 (depending on who you talk to and what materials you source). I have a currently running system that has cost me $1000 to date, and is just about to produce food. A third reason is the systems footprint. My system has about 4 times the grow area of a standard food computer (in fact, my system is almost better described as a “food server” in some regards). This means I can grow an actual useable crop. The standard food computer is a great opportunity to experiment, but the actual output would be pretty low as far as trying to feed myself. And thats my fourth reason, feeding myself. I have a lofty goal that someday I will grow 100% of my own food, so this is a step toward that goal (especially in the winter). I don’t eat meat, so veggies are the only thing I need to produce. Those of you that follow this blog will say “Hey, didn’t you write about eating the squirrels that plagued your camper?“, and you’d be right! Well, that was then, this is now, get over it (smiley face). Of course, going my own way has some disadvantages.
What are these disadvantages of which you speak?
Well, many of the problems have yet to surface, I’m sure. I’m on my first crop, so I have no idea what the final results will be. Will I get fruit at all? Will it taste like cat food? Who knows. A big problem is that my system is just one large system with one climate, one light cycle, and one nutrient spread. I have to be cautious what array of seeds I plant. If they require different nutrients or lighting, or have vastly different timing of growth stages, or different tolerances of heat, humidity and pH, it just won’t work. My idea of a constantly rotating crop (eating one crop while starting a new one) is likely to be impossible. I may have to do one crop, can/freeze/preserve it, and move to the next. Perhaps I will reserve its use to crops that cannot grow in my difficult climate, and stick to soil for others. It’s a lot of question marks that will only be answered with time and results.
The most important disadvantage is that my system limits the data and knowledge I can contribute back to the MIT project, which is open source. Wanting to support their open source initiative is my motivation to push myself to build a proper food computer ASAP.
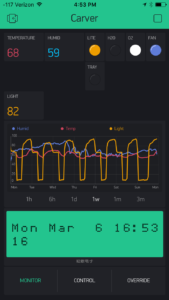
Cool story, just tell us about your setup already.
So it’s built with the Particle’s Photon microcontroller. It uses a temperature/humidity sensor (an AM2315), and a simple LDR to sense light levels. There is a propane furnace keeping it warm in our sub-zero temperatures. The brain (pictured above) uses a bank of relays to control two dual gang outlet boxes. The left 4 outlets are individually switchable, while the right are switched in pairs. This controls all of the pumps and lights and fans.
My code tells everything when to turn on and off. It can be overridden and manually controlled using an app called Blynk that talks to the system remotely and also allows me to monitor from afar. It texts me when the temperature drops low, alerting me to change the propane tank. That’s all setup using IFTTT.
In terms of hydroponic style, it’s a flood and drain system. The pump runs long enough to fill my tray, which then drains back to the holding tank. This keeps the roots wet and oxygenated. The water has a nutrient solution balanced for the needs of the plants. The water is oxygenated with a pump, much like a fish tank is. The pH is controlled via application of acids/bases depending on careful readings from a meter. I’m using a Hannah 98129 Combo meter that tests pH, Conductivity (EC), and Total Dissolved Solids (TDS). My grow light is an 8 tube, 40,000 lumen, T5 fluorescent unit by Agrobrite.

I started seeds on 1/20/17. By 1/31/17, I had seedlings ready to transplant. The seeds were started in rockwool cubes. The seedlings (cube and all) were then transplanted into net pots filled with an inert clay substrate. Every hour, the tray floods and drains. The light initially stayed on for 18 hours a day. Today, that changed to 12 hours a day. This is interpreted by the plants as the days getting shorter. It’s their cue to start flowering and producing fruit.
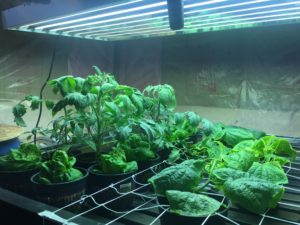
When my cucumbers began to reach out vines, I set dowels out to catch them, but today I switched that to a net trellis. I also switched my nutrients to a flower/bloom friendly variety. As you can see by the picture, I have come a long way from seedlings.
As always, anyone who would like to build something like this is welcome to my code, which I will probably place on GitHub at some point. Just email me from the contact page. I’ll write more when I start seeing fruit.
Nerdfarmers unite!